Knowledge Hub
High carbon ferro chrome manufacturer and supplier in Mumbai, Maharashtra, India

High carbon ferrochrome (HC FeCr) is an alloy of chromium and iron, with a higher carbon content, typically ranging from 4% to 8%. It is one of the most important materials used in the production of stainless steel and other alloy steels. Here are the primary uses of high carbon ferrochrome:
Stainless Steel Production
The main use of high carbon ferrochrome is in the production of stainless steel, particularly in the 200 and 300 series. It provides the necessary chromium content to stainless steel, which imparts corrosion resistance, strength, and hardness to the final product.
Carbon and Alloy Steel Production
High carbon ferrochrome is also used in producing various carbon and alloy steels. It adds chromium to the steel, enhancing its wear resistance, hardness, and overall durability. These properties are essential for applications like tools, machinery, and automotive components.
Casting and Foundry Applications
HC FeCr is used in casting and foundry applications to produce wear-resistant castings, such as rolls for rolling mills, grinding media, and crusher parts. The chromium content increases the hardness and wear resistance of these castings, making them suitable for demanding environments.
Hardfacing and Wear-Resistant Coatings
High carbon ferrochrome is used in hardfacing applications, where a layer of wear-resistant material is applied to the surface of metal components. This layer enhances the durability of the components in harsh operating conditions, such as in mining and construction equipment.
Manufacturing of Refractories
HC FeCr is used in the production of refractory materials, which are crucial for lining furnaces, kilns, and reactors. These refractories need to withstand high temperatures and corrosive environments, and the addition of chromium improves their performance and lifespan.
Production of High-Cr Content Alloys
HC FeCr is used in the production of high-chromium content alloys, such as high-chromium white irons and tool steels. These materials are used in applications that require excellent wear resistance, like in the production of crushing and grinding equipment.
Electric Arc Furnaces (EAF) and Induction Furnaces
In the steelmaking process, HC FeCr is added to the electric arc furnace (EAF) or induction furnace as a chromium source. It helps to achieve the desired alloy composition, particularly in the production of steel grades that require high chromium content
High carbon ferrochrome is essential for achieving the desired mechanical properties in a wide range of steel and alloy products, particularly in industries where durability, hardness, and corrosion resistance are critical.
Low carbon ferro chrome manufacturer and supplier in Mumbai, Maharashtra, India
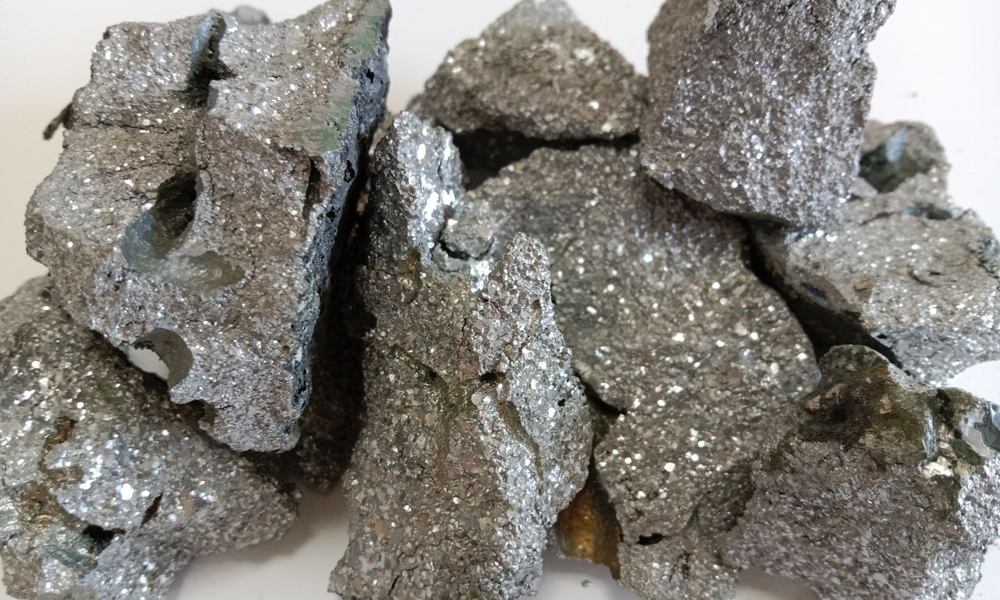
Low carbon ferrochrome (LC FeCr) is an alloy of chromium and iron with a low carbon content, typically less than 0.1%. It is primarily used in the production of stainless steel and other special steels where a high chromium content is desired without introducing much carbon. Here are some of the key uses of low carbon ferrochrome:
Stainless Steel Production
The primary use of low carbon ferrochrome is in the manufacturing of stainless steel. It is added to the steel to increase corrosion resistance, toughness, and hardness while maintaining a low carbon content, which is essential for certain grades of stainless steel like the austenitic (300 series) and ferritic (400 series) types.
Special Alloy Steels
Low carbon ferrochrome is used in the production of various special alloy steels that require a precise balance of chromium content without increasing the carbon content. These steels are used in applications that demand high strength, resistance to wear, and corrosion resistance.
Superalloys
In the aerospace and power generation industries, LC FeCr is used in the production of superalloys. These materials, which contain a mixture of elements including chromium, are used in high-temperature environments, such as gas turbine engines, due to their ability to maintain strength and resist oxidation and corrosion.
Welding Electrodes
Low carbon ferrochrome is used in the production of welding electrodes and fluxes. It helps maintain the required chromium content in the weld metal without introducing excessive carbon, which could lead to issues like carbide precipitation and reduced corrosion resistance in the weld zone.
Nickel Alloys
LC FeCr is used in nickel-based alloys, which are employed in industries like chemical processing, oil and gas, and marine engineering. These alloys benefit from the addition of chromium for enhanced resistance to high-temperature oxidation and corrosion.
Corrosion-Resistant Coatings
It is also used in the production of corrosion-resistant coatings for various industrial applications. The chromium in the alloy provides a protective layer that prevents oxidation and degradation of the underlying material.
Tool Steels
In tool steels, low carbon ferrochrome contributes to wear resistance and hardness, making it ideal for applications requiring sharp, durable cutting edges or tools that can withstand high stress.
Low carbon ferrochrome is critical in ensuring that high-performance steels and alloys meet specific mechanical and chemical requirements, especially in industries where material properties like corrosion resistance, hardness, and strength are paramount.
Ferro Silicon manufacturer and Supplier in Mumbai, Maharashtra, India
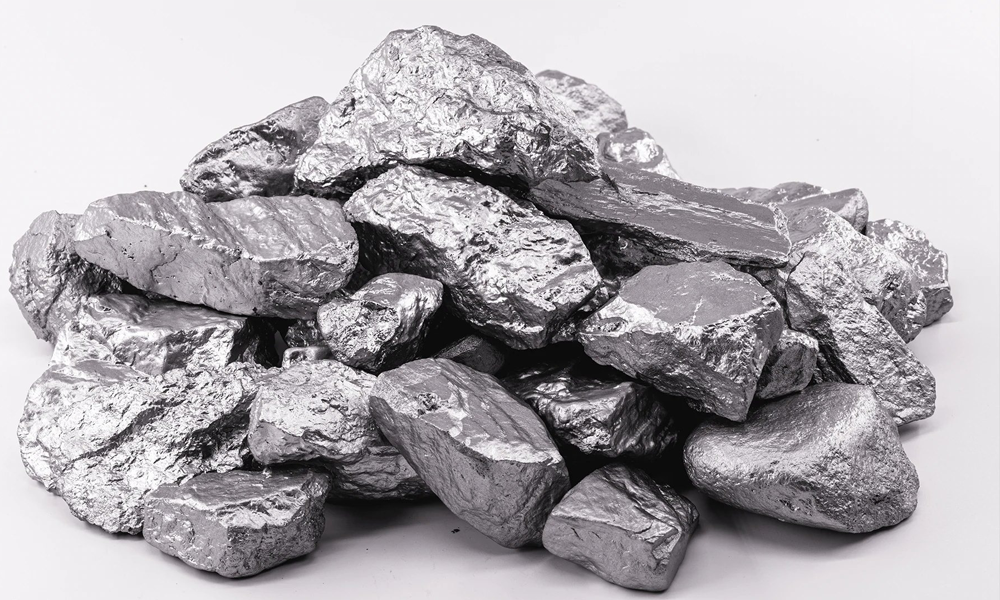
Ferro silicon is an alloy of iron and silicon, typically containing between 15% and 90% silicon. It is widely used in the steel and iron industries due to its various properties and benefits. Here are some of the key uses:
Deoxidizer in Steelmaking
Ferro silicon is commonly used as a deoxidizer in the steelmaking process. It helps remove oxygen from the molten steel, improving its quality and ensuring that the final product has the desired mechanical properties.
Inoculant in Cast Iron
In the production of cast iron, ferro silicon is used as an inoculant. It promotes the formation of graphite in gray cast iron, which improves its machinability and strength.
Alloying Agent
Ferro silicon is used as an alloying agent to improve the hardness and strength of steel. It is also used to produce silicon steel, which is essential for electrical transformers and motors due to its magnetic properties.
Reduction Agent in Production of Other Alloys
It acts as a reducing agent in the production of various ferroalloys, such as ferromanganese and ferromolybdenum, by reducing metal oxides to their metallic form.
Manufacture of Magnesium
Ferro silicon is used in the Pidgeon process for the production of magnesium, where it serves as a reducing agent.
Nodulizer in Ductile Iron
In the production of ductile iron, ferro silicon magnesium (a combination of ferro silicon and magnesium) is used to promote the formation of spheroidal graphite, which improves the ductility and toughness of the iron.
In the Production of Silicon
Ferro silicon can be used as a source of silicon in the production of pure silicon for use in semiconductors and solar panels.
Slag Coagulant
It helps in the formation of slag, which is a byproduct in steelmaking that floats on the surface of molten steel. This slag is removed to purify the steel.
These properties make ferro silicon an essential material in various metallurgical processes, contributing to the efficiency and quality of steel and iron products.
Graphite fines Supplier in Mumbai, Maharashtra, India
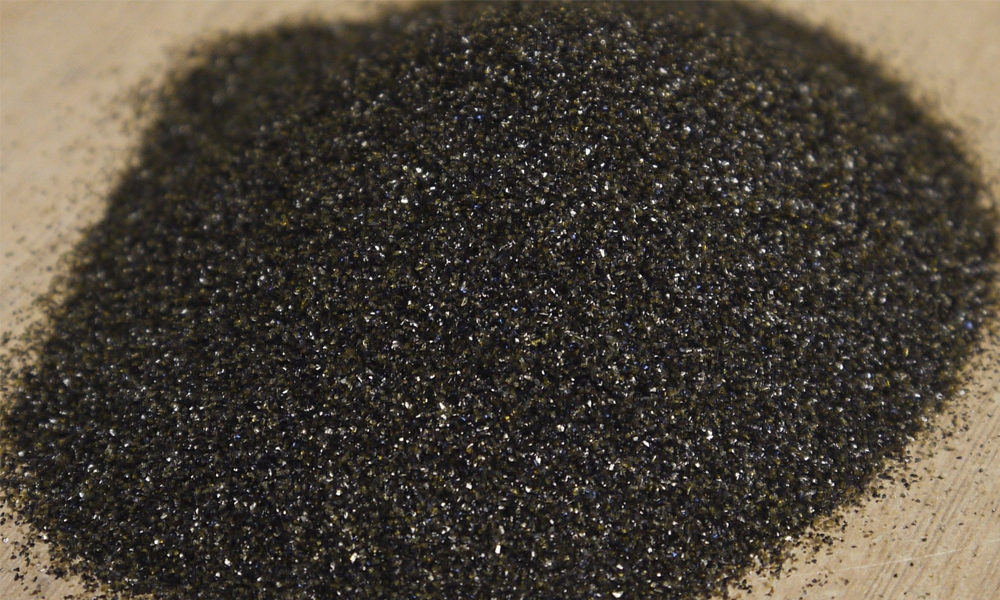
Graphite fines, also known as graphite powder or graphite dust, are small particles of graphite that result from the processing or machining of graphite materials. These fines have a range of industrial applications due to graphite’s unique properties, such as high thermal conductivity, lubricity, and resistance to corrosion. Here are some of the primary uses of graphite fines:
Lubricants
Graphite fines are widely used as a dry lubricant in various applications, especially in situations where wet lubricants (like oil) are not suitable. The fine particles reduce friction between moving parts, making them ideal for high-temperature applications, locks, and even precision instruments.
Refractory Materials
Graphite fines are used in the production of refractory materials, which are essential for lining furnaces, kilns, and other high-temperature industrial equipment. The addition of graphite improves the thermal shock resistance, mechanical strength, and overall durability of these materials.
Battery Manufacturing
In the production of batteries, particularly lithium-ion batteries, graphite fines are used as an anode material. The fine graphite particles provide a large surface area, which enhances the battery’s efficiency and capacity.
Conductive Materials
Due to its high electrical conductivity, graphite fines are used in the manufacture of conductive materials, such as conductive coatings, conductive adhesives, and electromagnetic interference (EMI) shielding materials.
Pencils and Art Supplies
Graphite fines are a key component in the manufacture of pencils. They are mixed with clay to produce the “lead” found in pencils, and the fine particles allow for smooth, consistent writing or drawing. Graphite powder is also used by artists for shading and other techniques.
Foundry Applications
In foundries, graphite fines are used as a parting agent or release agent. They prevent molds from sticking to the cast metal, ensuring clean, defect-free castings.
Metallurgical Applications
Graphite fines are used in various metallurgical processes, such as in the production of cast iron, where they serve as an inoculant to promote the formation of graphite flakes in gray iron, improving its machinability and overall quality.
Carbon Brushes
Graphite fines are used in the production of carbon brushes for electric motors. The fine graphite particles provide good electrical conductivity and lubricity, reducing wear on the brushes and the commutator.
Paints and Coatings
Graphite fines are added to certain paints and coatings to improve their thermal and electrical conductivity, as well as to provide a smooth finish. These coatings are often used in high-temperature environments or where conductive properties are required.
Seals and Gaskets
In the production of seals and gaskets, graphite fines are used to create materials that can withstand high temperatures and pressures while maintaining a good seal. The lubricating properties of graphite also help reduce friction and wear in these components.
Sintering and Powder Metallurgy
Graphite fines are used in powder metallurgy processes as a lubricant and to improve the sintering properties of metal powders. This helps in producing high-density, high-strength metal parts.
Graphite fines are versatile materials used across many industries due to their unique combination of lubricating, conductive, and refractory properties.
Manganese Mn Metal flake, Manganese Mn Metal briquettes Supplier in Mumbai, Maharashtra, India
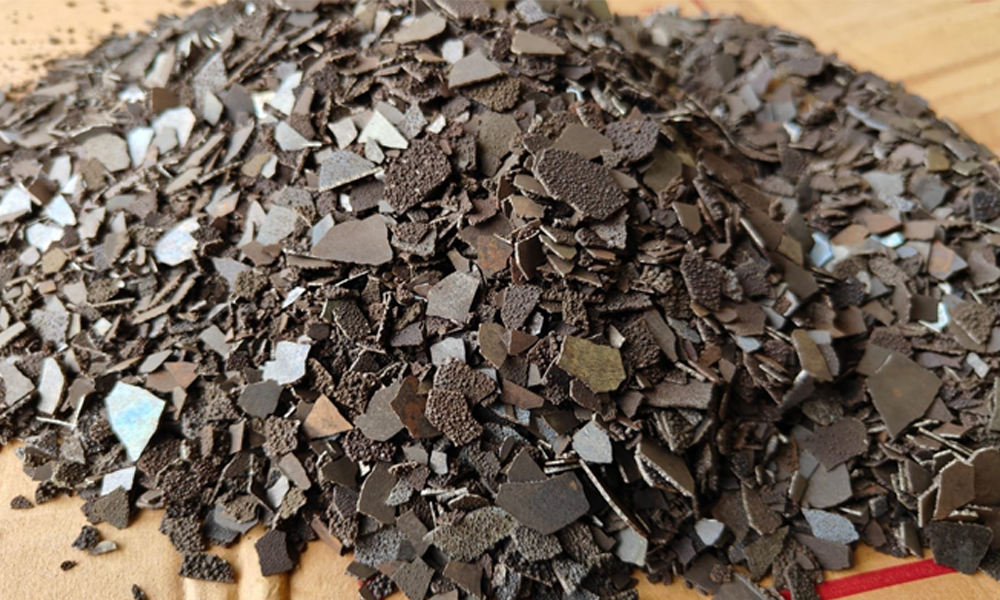
Manganese metal flakes are a form of manganese, a hard, brittle metal that is commonly used in various industrial applications. The metal is typically produced by electrolytic processes and is available in different forms, including flakes, powder, and ingots. Here are the primary uses of manganese metal flakes:
Steel Production
One of the most significant uses of manganese metal flakes is in the production of steel. Manganese is an essential alloying element in steelmaking because it improves the strength, toughness, and wear resistance of steel. It also acts as a deoxidizer and helps remove sulfur and oxygen impurities from steel, enhancing its quality.
Aluminum Alloys
Manganese is used in aluminum alloys to improve corrosion resistance and mechanical properties. Manganese metal flakes are added to aluminum to produce alloys used in applications like beverage cans, automotive parts, and construction materials.
Non-Ferrous Alloys
Manganese metal flakes are used in the production of various non-ferrous alloys, such as copper-nickel alloys. These alloys have improved strength, corrosion resistance, and thermal stability, making them suitable for applications in the marine industry, electrical components, and heat exchangers.
Battery Manufacturing
Manganese is used in the production of batteries, particularly in alkaline and lithium-ion batteries. In lithium-ion batteries, manganese is used in the cathode material (e.g., lithium manganese oxide), where it contributes to the battery’s capacity, stability, and overall performance.
Magnetic Alloys
Manganese metal flakes are used in the production of certain magnetic alloys, such as permalloy, which is used in the manufacture of transformers, inductors, and magnetic shielding materials. These alloys benefit from manganese’s ability to improve magnetic properties.
Chemical Production
Manganese is used as a catalyst in the chemical industry, particularly in the production of potassium permanganate, a powerful oxidizing agent used in water treatment, organic synthesis, and as a disinfectant.
Foundry Applications
Manganese metal flakes are used in foundries to produce cast iron and steel castings. Manganese helps improve the toughness and wear resistance of these castings, making them suitable for use in heavy-duty industrial applications.
Specialty Stainless Steels
Manganese metal flakes are used in the production of specialty stainless steels, where they replace or supplement nickel. These manganese-rich steels are used in applications where high strength and good corrosion resistance are required, such as in marine environments or in construction.
Pigments and Dyes
Manganese compounds derived from manganese metal flakes are used as pigments in ceramics, glass, and paints. For example, manganese dioxide is used to create brown and black pigments.
Welding Rods and Electrodes
Manganese metal flakes are used in the production of welding rods and electrodes. Manganese is added to improve the toughness and strength of the weld metal, and to prevent cracking.
Manganese metal flakes are critical in various industries, particularly in metallurgy, where they play a key role in improving the properties of alloys and enhancing the performance of various metal products.